Choosing the Right Mould Temperature Controller: Key Features and Benefits
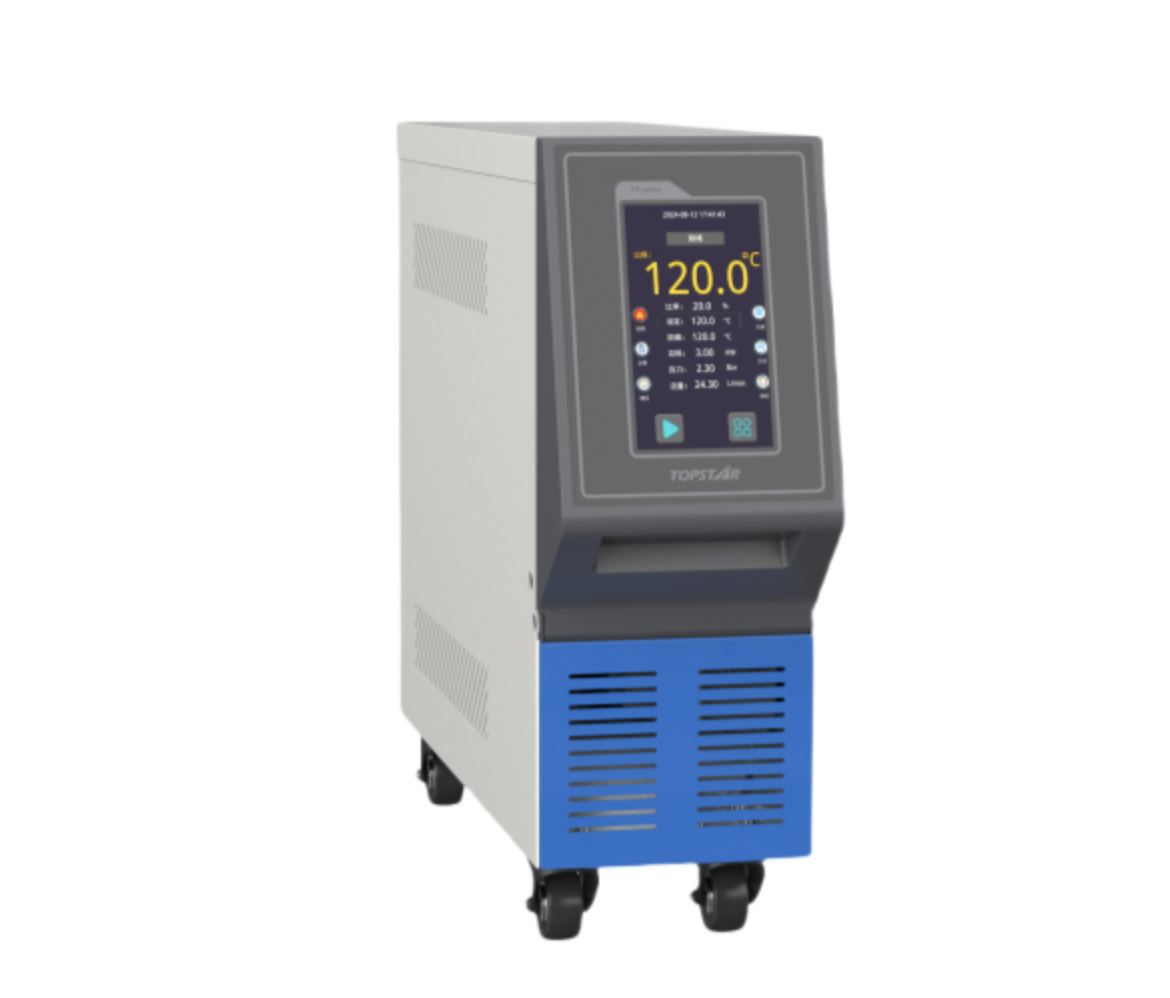
Selecting the suitable mould temperature controller (MTC) for your plastic injection moulding operation is crucial to achieving optimal performance, energy efficiency, and product quality. A well-chosen MTC can significantly impact productivity, cost savings, and part consistency, given the importance of temperature regulation in ensuring smooth moulding processes.
In this guide, we will explore the key features you should consider when selecting a mould temperature controller, the benefits of using one in your production line, and how to make an informed decision.
Importance of Mould Temperature Control
Mould temperature controllers play a vital role in the plastic injection moulding process by managing the temperature of the mould to ensure uniform heating and cooling. This temperature regulation is essential for several reasons:
Consistent Product Quality: Accurate temperature control ensures uniform cooling of parts, reducing defects like warping, surface imperfections, and sink marks.
Reduced Cycle Time: By optimizing the mould’s temperature, MTCs help shorten cooling times, reducing the overall cycle time for each part.
Energy Efficiency: MTCs minimize energy wastage by maintaining an optimal temperature range without unnecessary heating or cooling.
Extended Mold Life: Precise control of mould temperature reduces thermal stress on the mould, prolonging its lifespan and reducing maintenance costs.
Given these benefits, selecting the right MTC is essential to optimizing your production process.
Key Features to Consider When Choosing a Mould Temperature Controller
Heating and Cooling Capacity
The heating and cooling capacity of an MTC is a fundamental feature that dictates how well it can manage the mould’s temperature. These capacities are typically measured in kilowatts (kW) and reflect the unit’s ability to bring the mould to the desired temperature and maintain it under different operating conditions.
Higher heating capacities are necessary for operations that require rapid heating or deal with large moulds. On the cooling side, the system must efficiently remove excess heat from the mould after injection to prevent overheating.
Key Consideration: Evaluate the size and complexity of your mould and choose an MTC that matches your heating and cooling needs. A mismatch in capacity could lead to inconsistent temperature control and longer cycle times.
Temperature Range
The temperature range an MTC can handle is crucial, as different materials and processes require different temperature settings. Some plastics, like ABS or polycarbonate, require higher mould temperatures, while others, like polypropylene or polyethene, need lower settings.
Choose a mould temperature controller with a broad temperature range to accommodate your specific material requirements. Advanced MTCs can maintain mould temperatures from as low as 30°C (86°F) to as high as 160°C (320°F) or more.
Key Consideration: Select an MTC that offers sufficient temperature flexibility for your current processes and potential future projects that may involve different materials.
Read more : Childhood Friend Complex Manga
Accuracy and Precision
One of the primary advantages of a good MTC is its ability to maintain the mould temperature within a tight range. Temperature fluctuations, even slight ones, can lead to part defects, inconsistent quality, or longer cooling times.
Modern MTCs come equipped with digital controllers and precise temperature sensors that monitor and regulate the mould temperature accurately, with tolerances as acceptable as ±1°C (±1.8°F). This level of precision ensures optimal process control and consistent part quality.
Key Consideration: Look for an MTC with high precision and reliable temperature sensors. Accuracy is critical to achieving consistent results, mainly when working with complex or high-precision moulds.
Control Interface
The user interface and control panel of an MTC are essential factors that influence ease of operation. Many modern MTCs come equipped with digital displays, touchscreens, and intuitive control systems that allow operators to monitor temperature, adjust settings, and diagnose issues quickly.
Advanced systems may also offer remote monitoring capabilities, allowing operators to oversee multiple MTCs from a central location and improving efficiency across large-scale production environments.
Key Consideration: To minimize downtime and errors, choose an MTC with a user-friendly interface and features like programmable temperature settings, remote monitoring, and real-time alerts.
Type of Heat Transfer Fluid
Mould temperature controllers typically use water or oil as the heat transfer fluid. Water-based MTCs are ideal for applications requiring moderate temperature ranges, typically between 30°C (86°F) and 95°C (203°F). For higher temperature applications, oil-based systems are preferred because oil has a higher boiling point and can withstand temperatures beyond 150°C (302°F).
Key Consideration: Choose the heat transfer fluid best suits your operational needs. Water-based systems are energy-efficient and cost-effective for lower-temperature applications, while oil-based systems are more suited for high-temperature moulding.
Safety Features
Safety is critical in any industrial environment, and MTCs are no exception. Reliable temperature controllers should have multiple safety features to prevent overheating, leaks, or equipment failure. Some standard safety features include:
Overtemperature Protection: Automatically shuts down the system if the mould temperature exceeds a pre-set limit.
Pressure Relief Valves: Protect the system from overpressure, particularly in oil-based units.
Leak Detection: Ensures quick identification and response to any coolant leaks in the system.
Key Consideration: Ensure your chosen MTC has built-in safety features to protect your equipment and personnel.
Maintenance and Serviceability
Like any other equipment, mould temperature controllers require regular maintenance to ensure they perform optimally. Look for systems that are easy to maintain and come with readily available replacement parts.
A well-maintained MTC will perform more efficiently, last longer, and result in fewer interruptions to production.
Key Consideration: Opt for MTCs with a reputation for reliability and low maintenance requirements, and ensure the manufacturer offers good customer support and service options.
Benefits of Using the Right Mould Temperature Controller
Investing in a suitable mould temperature controller for your production line provides a range of benefits, including:
Improved Product Quality
An effective MTC ensures uniform heat distribution across the mould, reducing the likelihood of defects and ensuring each part is produced to specification. This results in fewer rejected products and a more consistent output.
Increased Efficiency
By optimizing mould temperature, an MTC helps reduce cooling times and improve overall cycle times, allowing you to produce more parts in a shorter time. This increase in throughput can have a significant positive impact on overall productivity.
Energy Savings
Modern MTCs are designed to operate efficiently, using only the necessary energy to maintain the mould temperature. This helps reduce overall energy consumption, lowering operating costs over time.
Reduced Downtime
Accurate temperature control ensures that the mould operates consistently within optimal conditions, reducing the likelihood of production issues or breakdowns. When combined with remote monitoring and diagnostics, MTCs can minimize unplanned downtime and help resolve problems quickly.
Prolonged Mold Life
Precise temperature management reduces thermal stress on the mould, extending its lifespan and reducing the need for costly replacements or repairs. Keeping the mould within a stable temperature range minimises wear and tear on this critical component of your production line.
Choose the appropriate mold temperature controller
Choosing the suitableauld temperature controller is essential for optimizing your plastic injection moulding process. By focusing on key features like heating and cooling capacity, temperature range, accuracy, and safety, you can select an MTC that enhances efficiency, improves part quality, and reduces operational costs.
With the proper mould temperature controller, your production line will benefit from consistent results, reduced cycle times, and a more reliable moulding process.